In this article, we focus on bridging the knowledge gap needed for making an informed spindle selection by examining two critical variables: machining time and material removal rate (MRR). While spindle power is often seen as the key factor in CNC performance, understanding how it influences machining time and MRR is essential for making the right decision on spindle size. We’ll explore how spindle power affects the speed at which material is removed and how this, in turn, shapes the overall efficiency of a CNC project. By examining trends in machining time across different spindle power levels, we can better understand how these variables come into play and why they are crucial for fine-tuning your spindle selection.
Material Removal Rate
The material removal rate (MRR) refers to how much material the CNC can cut away over a given period, typically measured in volume per time (e.g., cubic inches per minute). It is a crucial metric in CNC machining because it directly impacts the efficiency of the process. A higher MRR indicates that more material is being removed in a shorter time, which is often desirable for maximizing productivity. However, increasing MRR can also lead to higher tool wear, greater heat generation, and reduced surface quality if not carefully managed.
Axial Depth of Cut
The axial depth of cut (ADOC) and radial depth of cut (RDOC) are two important factors that define the extent of material removal during a CNC machining operation. The axial depth of cut refers to how deep the cutting tool penetrates into the material along the axis of the tool, or in other words, the vertical depth of the cut. It directly affects the load on the tool in the axial direction, influencing factors like tool wear and heat generation.
Radial Depth of Cut
On the other hand, radial depth of cut refers to the width of the material being removed in each pass, or how much of the tool’s diameter is engaged with the work piece. It affects the load on the tool in the radial direction, impacting the overall material removal rate and the lateral forces applied to the tool. In CNC operations, balancing the ADOC and RDOC is crucial for maximizing efficiency and tool life, as aggressive settings in either direction can lead to excessive wear, tool breakage, or poor surface finishes.
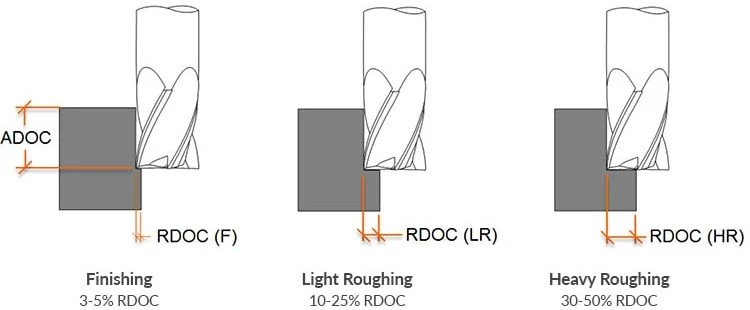
Material Removal Rate vs Feed Rate
MRR is a measure of how much material is being removed from a workpiece over time, typically measured in cubic inches per minute (in³/min) or cubic millimeters per minute (mm³/min). It accounts for the volume of material removed, considering both the feed rate – how fast the tool moves through the material in inches per minute (in/min) or millimeters per minute (mm/min), and the depth of cuts – how deep and wide the tool is cutting in inches (in) or millimeters (mm). The formula for calculating MRR can be expressed as:

Material Removal Rate vs Chip Load
Chip load, on the other hand, focuses on the material removed by each cutting edge of the tool per revolution. It refers to the thickness of the chip produced during each pass of a flute on the tool. Think of it as a more micro-level view, telling you how much material is being removed per cutting edge during each revolution. MRR gives you the macro view, telling you how much total material is removed over a set period. It takes into account both the axial and radial depth of cut, which are not considered in the chip load calculation.
While chip load doesn’t directly include radial depth of cut (RDOC), it indirectly influences the RDOC because an increase in RDOC increases the cutting tool’s engagement, which in turn increases the chip thickness and force on each cutting edge. Therefore, though MRR and chip load are related, they serve different purposes. Chip load is used to optimize tool life and cutting efficiency, while MRR is a measure of productivity (how fast material is removed).
Relationship Between Spindle Power and Material Removal
When selecting the right spindle for your CNC machine, one of the most important considerations is spindle power. While it’s easy to assume that more power always means better performance, it’s crucial to understand the relationship between spindle power and material removal rate—and more importantly, how increasing spindle power yields diminishing returns.
To fully grasp the impact of spindle power, it’s important to consider how power translates into material removal. This involves more than just increasing the spindle’s horsepower—factors like material hardness and the cutting conditions play a critical role in determining the efficiency of the spindle. As we delve deeper, understanding the Power Constant (‘P’) becomes essential for estimating how spindle power influences machining time across different materials and processes.
Power Constants
The time it takes to machine a given material is directly influenced by the power of the spindle, the material’s hardness, and the specific cutting conditions, such as finishing or roughing. One of the most important variables in determining how long a machining operation will take is the Power Constant (‘P’), which reflects the power required to remove material at a given rate. This constant varies depending on the material and cutting process, helping us understand how spindle power impacts the duration of machining tasks. This power constant value is highly dependent on the material being machined, as different materials have different hardness and machinability properties. The table below illustrates the different Power Constant values of varying materials:
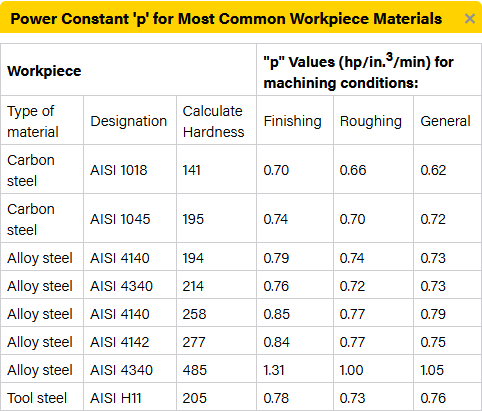
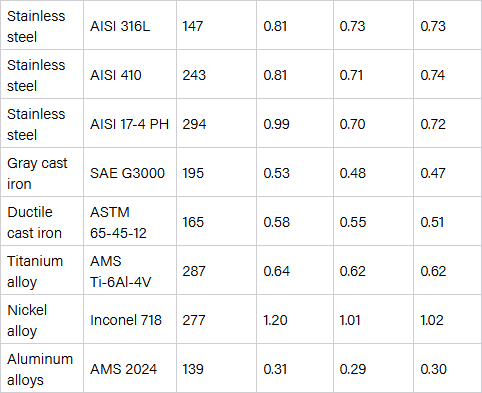
After reviewing the chart, we can observe that power constant values for materials such as steel and aluminum are readily available due to their importance in industrial machining. However, for materials like wood, power constant values are rarely published or easily found online. This is primarily because these calculations are often either academic or used to demonstrate relationships between spindle power and material removal rates, which are more relevant for industrial applications. In contrast, CNC users working with wood typically focus on hobbyist or small-scale projects where these kinds of calculations are less crucial.
That being said, we can estimate a predicted value for wood’s power constant by extrapolating from the values given for aluminum and softer metals. Based on the trend, where softer materials require less power for removal, we can predict a power constant for wood in the range of 0.05 to 0.10 hp/in³/min for roughing operations. This estimation means that less spindle power will be needed to remove a given volume of wood compared to aluminum or metals, making it more efficient in terms of material removal rate (MRR).
Calculating Machining Time with Power Constants
To determine the machining time for different spindles, we need to know the material removal rate – volume of material removed per unit time, spindle power – actual power delivered by the spindle, and power constant – amount of power required to remove one cubic volume of material per time. The formula to calculate Material Removal Rate (MRR) is provided below, where multiplying the spindle power (in kilowatts) by 1.341 converts it to spindle power (in horsepower):

It’s important to note that this equation differs from the typical MRR formula that factors in axial depth, radial depth of cut, chip load, and spindle RPM, and can be seen above. While both approaches yield the same MRR value, this method leverages spindle power, enabling us to assess how changes in spindle power influence material removal rates and ultimately operation time. This approach offers a clearer understanding of the impact of increasing spindle size on cutting efficiency. Now, once we have the MRR, we can estimate the machining time for any given operation by dividing the total volume of material to be removed by the material removal rate (MRR):

Using these equations, we can generate a table illustrating the trends in material removal rates and the corresponding machining times by varying spindle powers while keeping the volume of material constant across all scenarios. For this comparative analysis, we will assume the material being milled has dimensions of 30″ x 20″ x 0.5″, giving us a total volume of 300in³. This approach allows us to compare how different spindle powers affect the time it takes to mill the same amount of material under consistent conditions.
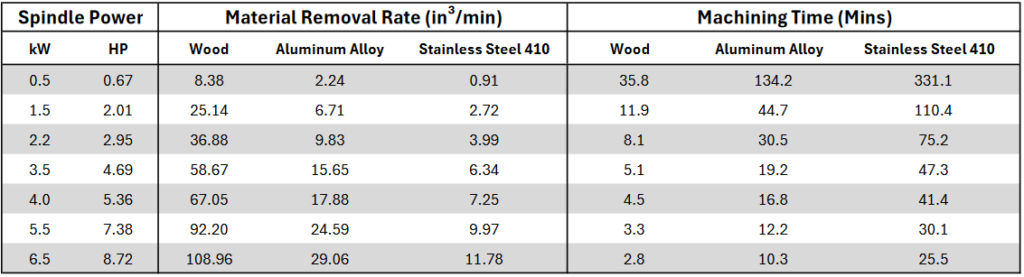
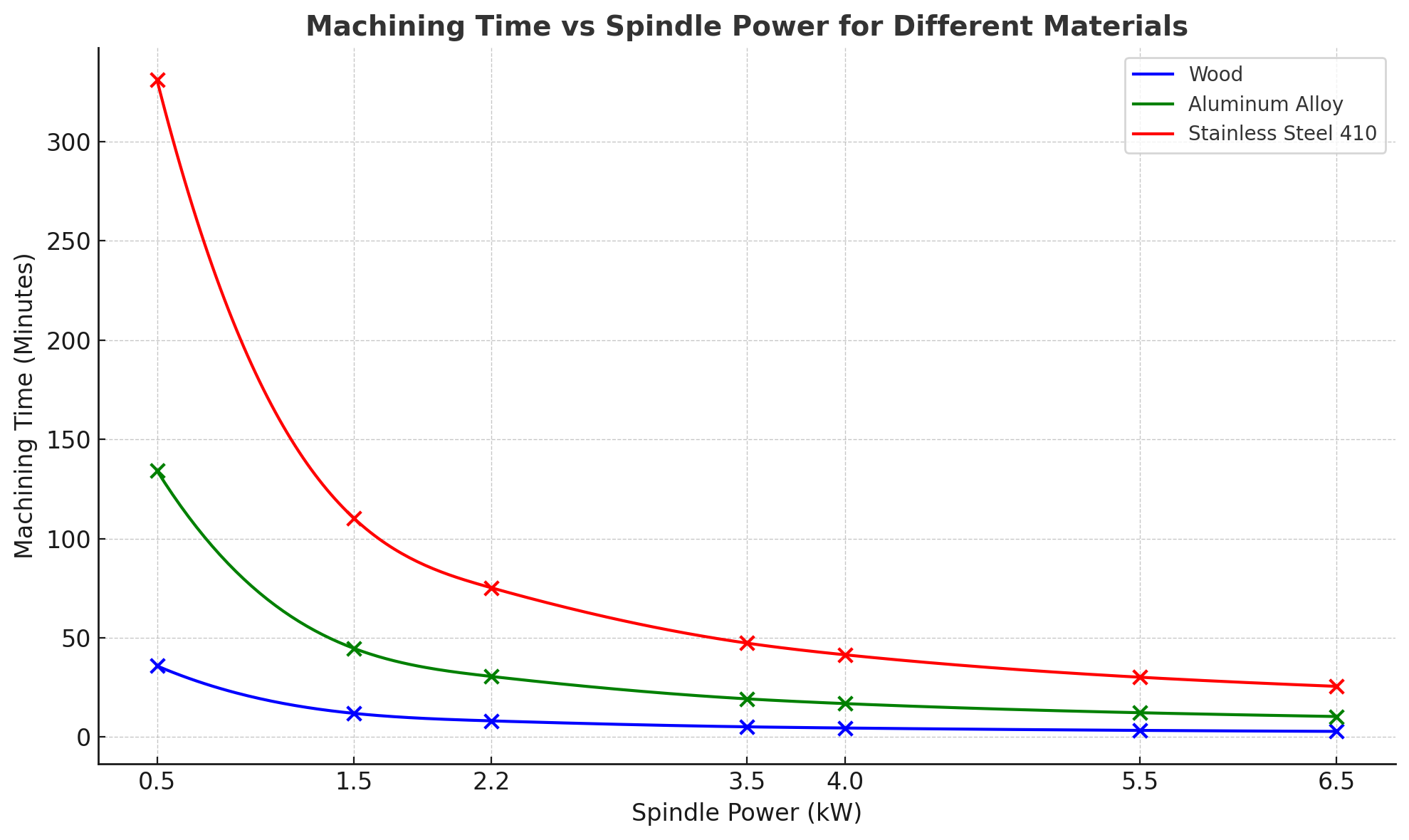
The relationship between spindle power and machining time is clearly inversely proportional, as shown in the chart. When spindle power increases, the machining time decreases, reflecting the expected trend. However, what’s especially notable is the rate at which machining time decreases — it follows an exponential decay. This means that while the initial jump in spindle power results in a significant reduction in machining time, further increases provide diminishing returns.
For instance, upgrading your spindle from 0.5 kW to 1.5 kW dramatically cuts machining time by about a third across all materials, reducing the time for wood by over 24 minutes. However, moving from a 1.5 kW to a 2.2 kW spindle only shaves off an additional 4 minutes for wood. This trend demonstrates that while boosting spindle power does cut down machining time, the amount of time saved becomes less significant with each successive increase in power, which showcases the diminishing returns of investing in higher spindle power.
Based on the trend shown in the graph, a 1.5 kW spindle appears to be more than sufficient for a hobbyist like myself, particularly when comparing the machining times for wood and aluminum. While a 0.5 kW spindle takes significantly longer to complete tasks, upgrading to 1.5 kW drastically reduces machining time, offering substantial improvements. However, further increases in spindle power, such as moving to a 2.2 kW or 3.5 kW spindle, don’t yield dramatically faster results. The additional time savings are minimal compared to the jump from 0.5 kW to 1.5 kW. While considerations like torque, power, and machine stability are separate issues, in terms of pure machining time, a 1.5 kW spindle strikes a solid balance between performance and efficiency without the diminishing returns seen with more powerful spindles.
Key Takeaways
- Diminishing Returns in Power Increases: The diminishing returns when upgrading beyond 1.5 kW are evident. While a 2.2 kW spindle does offer marginal time savings, the difference is minimal—just a few minutes of gain for a considerable increase in power and complexity.
- Contextual Relevance for Hobbyists: For a hobbyist operating out of a home workshop, where projects tend to be smaller-scale and time isn’t necessarily the most critical factor, a 1.5 kW spindle offers a reliable middle ground.
- Torque and Stability Considerations are Separate: While this discussion focuses on machining time, it’s important to acknowledge that other factors—such as torque, spindle stability, and motor efficiency—may also influence spindle selection, in which we have deduced from the previous articles that 1.5kW may not be enough for aluminum.