In the last parts of this series, we explored the foundational aspects of CNC machine design, focusing on the material properties that influence rigidity, vibration dampening, and structural integrity. Additionally, we delved into linear guide and motion drive systems, both critical for ensuring smooth, accurate movement. These factors together play a crucial role in determining the machine’s precision, stability, and overall performance.
In this part of the series, we shift our attention to one of the most critical components of the entire system — the spindle. Its importance cannot be overstated, as the performance and success of your entire CNC machine hinges on a thorough understanding of this critical element. In this article, we’ll explore everything you need to know about CNC spindles to make an informed decision. From spindle power and bearings to cooling systems and power requirements, we’ll cover the essential factors that will help you optimize your machine for your specific machining needs.
What's a CNC Spindle?
A CNC spindle is the driving component responsible for the rotation of the cutting tool in a CNC machine. It plays a central role in the machining process by powering the tool that cuts, mills, drills, or grinds the material. At its core, the spindle is a motorized shaft that holds the cutting tool and rotates at variable speeds, delivering the necessary torque and precision for various operations. In essence, it is the heart of any CNC machine, controlling the interaction between the cutting tool and the material, which directly impacts the quality of the work produced.
The spindle’s importance cannot be overstated, as it dictates several key elements of the machining process, including cutting speed, feed rate, torque, and overall cutting accuracy. An underpowered or improperly chosen spindle can result in poor surface finishes, material deformation, excessive tool wear, and even machine failure. On the other hand, a well-matched spindle allows the CNC machine to operate efficiently, with minimal downtime and superior results.
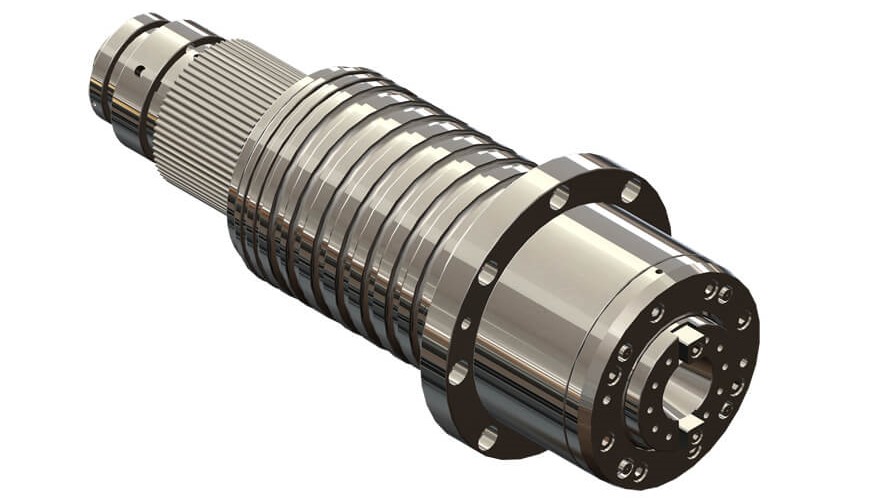
From a technical standpoint, spindles are challenging components because they need to balance multiple factors, such as speed, power, torque, and precision, often within a confined space. They are expected to handle various materials—ranging from soft woods to hard metals—at different speeds and forces while maintaining accuracy. Spindles must also withstand the mechanical stresses generated during high-speed operations, maintain smooth rotation, and dissipate heat to prevent overheating. Additionally, they need to be compatible with a range of tools, collets, and end mills to provide versatility in operations.
These factors make spindle selection one of the most technically complex aspects of CNC machine design, as each spindle is tailored to specific applications. Choosing the right spindle is critical for achieving optimal machining performance, and understanding its role is the first step in ensuring your CNC machine operates at its full potential.
Spindle Power: The Deciding Factor For Spindle Size
Spindle power refers to the amount of energy the spindle motor can deliver to drive the cutting tool through the material. It is usually measured in kilowatts (kW) or horsepower (HP), and it directly influences the spindle’s ability to handle different materials and operations. The spindle power essentially determines how efficiently the CNC machine can cut through various materials, from soft woods to harder metals like aluminum and steel.
The power of a spindle affects two main factors: cutting speed and torque. Higher spindle power allows for faster cutting speeds and better material removal rates, while also providing the necessary torque to cut through tougher materials. If the spindle lacks sufficient power, it will struggle to maintain performance, leading to poor cutting quality, overheating, excessive tool wear, and reduced productivity.
Spindles come in a range of sizes and specifications, but they are typically discussed in terms of their power output, which serves as the primary reference point in most conversations. Choosing the right spindle size for your CNC machine depends heavily on the scale of your projects and the materials you’ll be working with. Spindles range in size from compact units for desktop CNCs to heavy-duty industrial spindles designed for large-scale operations. Each size category has its advantages and limitations, and making the right choice is essential for optimizing machine performance. As a clear rule of thumb: The spindle power should match the hardest material you intend to cut. Opting for higher power gives you more flexibility but will increase both cost and power consumption.
Small Spindles (0.5 kW – 1.5 kW)
Small spindles within this range are typically used in hobbyist machines for light-duty tasks, particularly with wood and other softer materials. These spindles are lightweight, easy to integrate into smaller setups, and affordable. They are ideal for hobbyists or small-scale projects where precision is important, but heavy cutting forces are not required. While smaller spindles can be effective for detailed woodwork, they generally lack the power needed for aluminum machining. Attempting to use a smaller spindle for aluminum can lead to inadequate cutting power, tool stalling, and poor surface finishes.
While these lower-power spindles don’t exert the same cutting forces as mid-range or industrial spindles, the machine’s frame must still be designed to handle the movement and torque during operations. A more flexible or unstable frame may result in inaccuracies, particularly when precision is required.
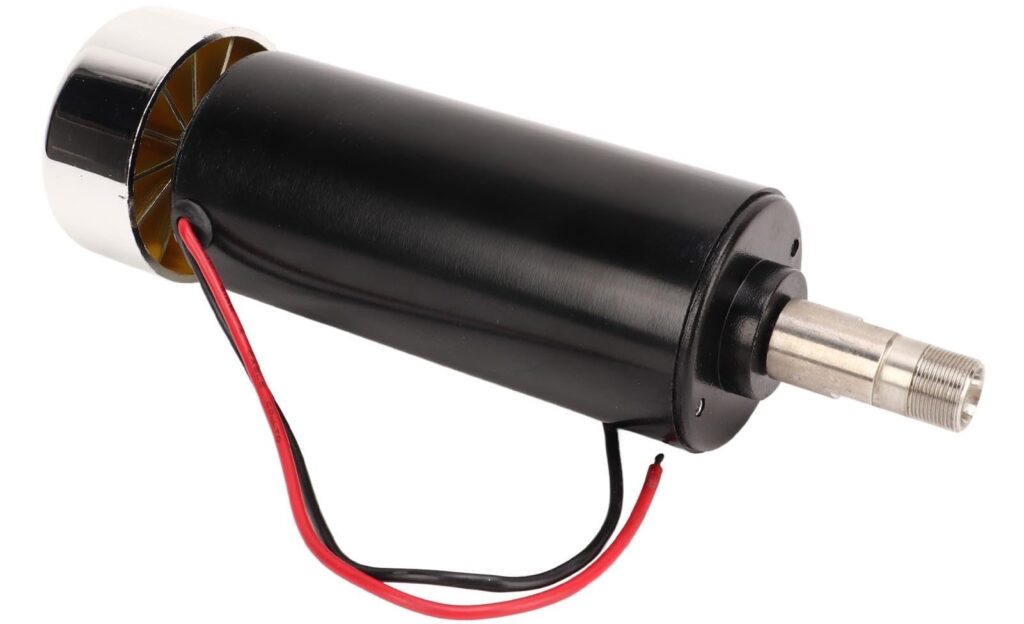
Lower Mid-Range Spindle (1.5 kW)
This spindles strike a balance between affordability and performance, making them well-suited for users working primarily with wood, plastics, and occasional light metal machining like aluminum (if they are feeling very bold to the task). However, as the demands of aluminum machining increase—such as in terms of material thickness or hardness—the limitations of medium spindles may become apparent, particularly if the machine’s rigidity isn’t up to the task.
Common in hobbyist and small workshop CNC machines, it provides adequate cutting power and torque for most projects, while still being relatively easy to install and maintain. Its power output is enough to handle moderately demanding tasks without requiring overly complex setups or cooling systems.
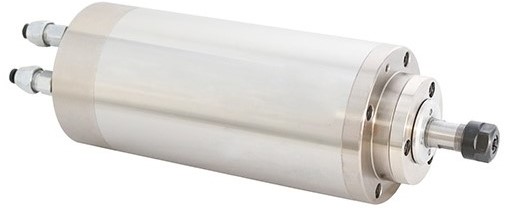
Upper Mid-Range Spindles (2.2 kW – 3.5 kW)
Spindles in this range offer more cutting power and torque, making them better suited for users who need to machine a broader range of materials, including tougher metals like aluminum. These spindles are typically found in semi-professional CNC machines or small business setups and can manage tougher materials and deeper cuts with greater ease. While they come with a higher price tag and require enhanced cooling solutions, they deliver the versatility and efficiency needed for more demanding projects, making them ideal for users looking for a high-performing spindle without the complexities of industrial-grade setups.
However, it’s important to note that as spindle size increases, so does the demand for a more robust machine structure. The increased power and torque exerts more force on the machine’s frame, requiring it to be rigid and stable to maintain precision and avoid deflection or vibrations.
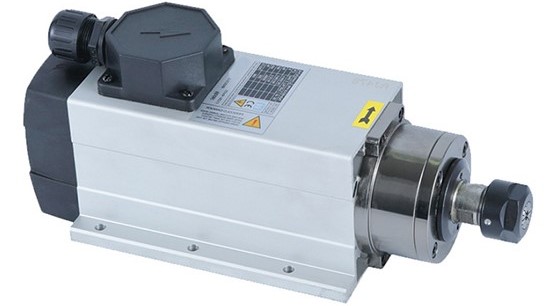
Large Industrial Spindles (3.5 kW – 10 kW+)
Large industrial spindles are designed for high-performance CNC machines used in industrial settings. These spindles are built to handle hard materials like steel and titanium, as well as large-scale operations requiring continuous, high-torque performance. While industrial spindles deliver exceptional power and precision, they are significantly more expensive, bulkier, and require advanced cooling and maintenance systems. These spindles are suited for large-scale manufacturing or fabrication processes but are often excessive for smaller or less complex projects.
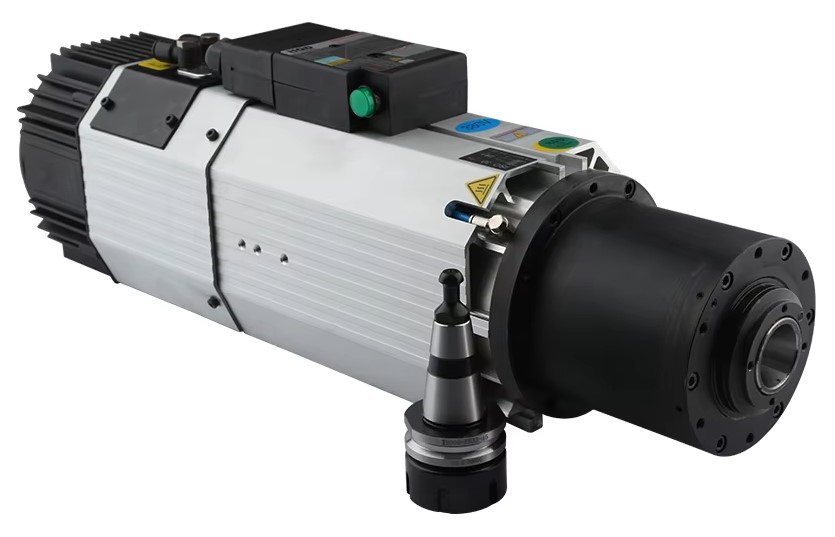
In summary, when selecting a spindle, it’s essential to consider not just the power requirements, but also the capabilities of your CNC machine’s frame and motion system. A well-balanced machine, with a spindle that matches its structural strength and intended use, will perform more reliably and produce better results, whether you’re working with wood, aluminum, or a combination of both.
Spindle Bearings: A Consideration For Greater Handling
Bearings are essential components within a CNC spindle that directly affect its precision, durability, and overall performance. They provide support to the rotating spindle shaft and effectively handle both radial (side-to-side) and axial (up-and-down) forces that are generated during the machining process. These forces can vary significantly depending on the materials being cut and the type of machining operations being performed. The bearings ensure that the spindle maintains smooth and stable rotation under these stresses, allowing for precise cuts and reducing the risk of tool deflection or spindle failure.
The type of bearing used in a spindle is crucial, as it determines the spindle’s ability to reduce friction, absorb loads, and maintain cutting accuracy under different operational conditions. High-quality bearings enhance the spindle’s lifespan and performance by minimizing wear and ensuring that the cutting tool remains firmly in place, even during heavy-duty machining operations. On the other hand, poor-quality or improperly selected bearings can result in excessive vibration, poor surface finishes, and premature wear of both the tool and the spindle itself.
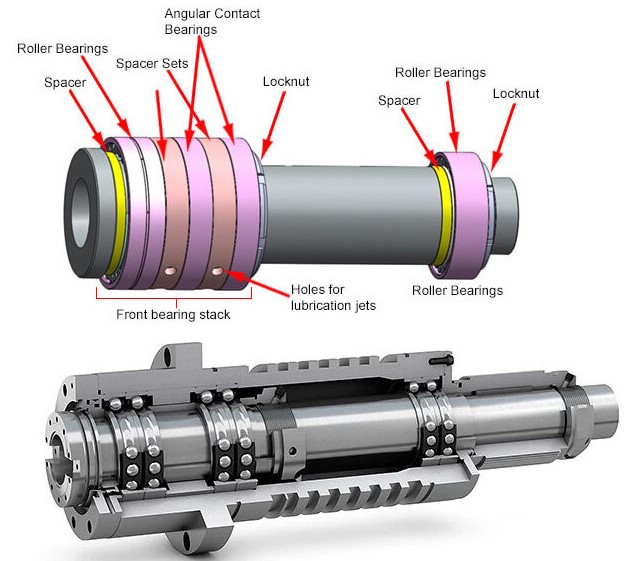
Ball Bearings: Common but Limited
Ball bearings are the most widely used type of spindle bearing, offering a good balance of speed, precision, and affordability. These bearings are ideal for general-purpose CNC machining where moderate cutting forces are applied. Ball bearings work by allowing the spindle shaft to rotate with minimal friction, but their ability to handle high loads—particularly axial loads—has its limits. This makes them best suited for light-duty CNC machines, typically those used for wood, plastics, and sometimes for softer metals like aluminum.
One of the advantages of ball bearings is their high-speed capability, which is why they are often used in spindles that require relatively high RPMs. However, in more demanding industrial applications where prolonged use and heavy loads are common, ball bearings may wear out faster and require more frequent maintenance or replacement.
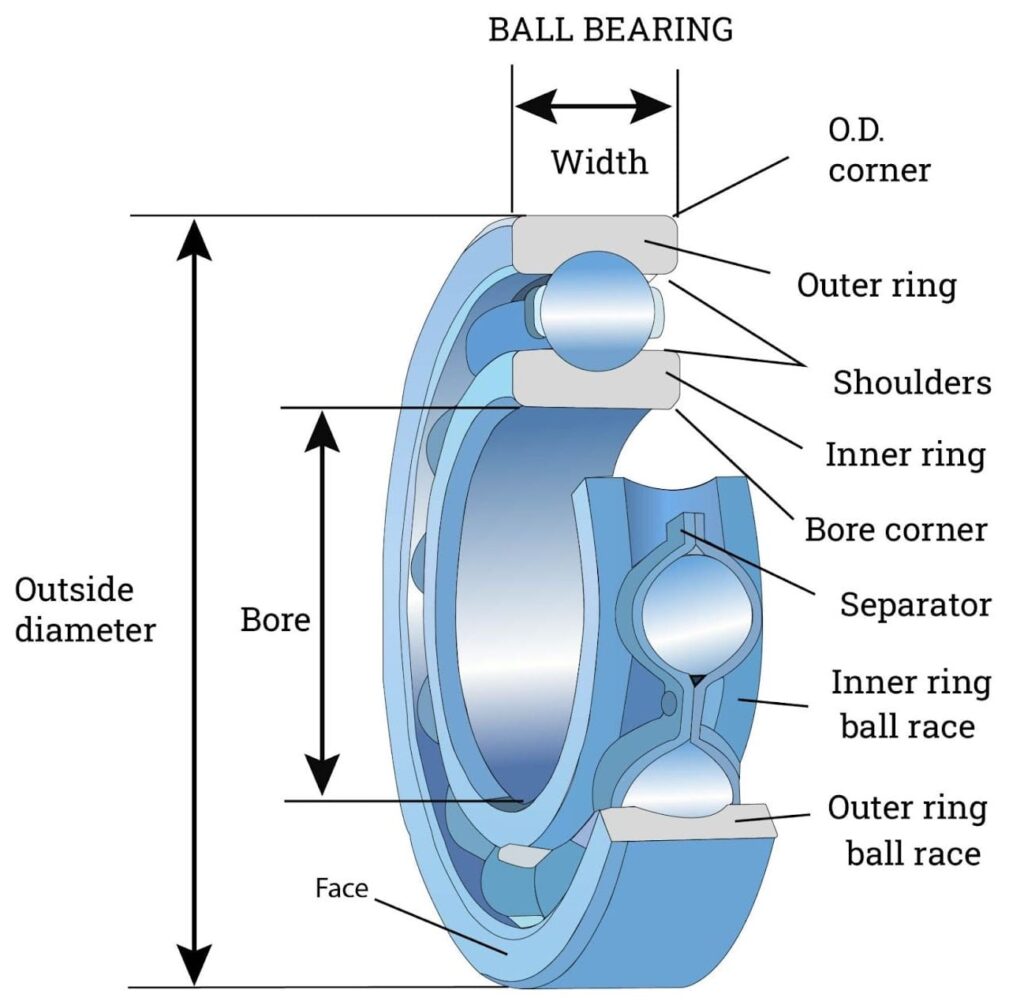
Tapered Roller Bearings: Heavy-Duty Performance
Tapered roller bearings are designed to handle heavier radial and axial loads, making them a more robust option for high-performance CNC applications. Unlike ball bearings, which distribute loads evenly around their circumference, tapered roller bearings have a conical shape that allows them to support high loads in a specific direction. This design makes them ideal for spindles that will be cutting harder materials like steel or for machines that require deep, forceful cuts in aluminum.
The higher load capacity of tapered roller bearings comes at the expense of some speed, as they typically have a lower maximum RPM compared to ball bearings. However, for applications that prioritize durability and stability over speed—such as heavy-duty metal machining—tapered roller bearings are a far better choice. Their ability to withstand both radial and axial forces with greater durability ensures long-lasting performance under tough conditions.
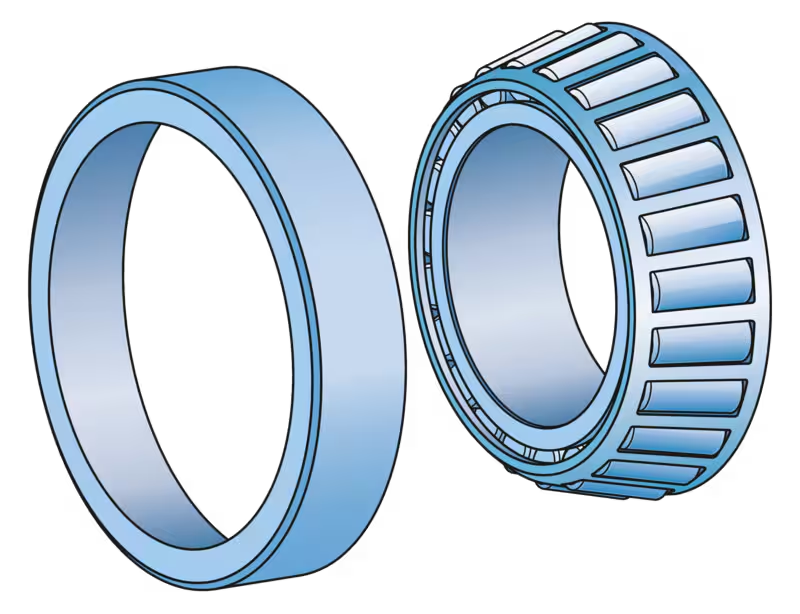
Ceramic Bearings: High Precision, High Speed
Ceramic bearings are typically found in high-speed, high-precision spindles. These bearings use ceramic balls, which are harder and smoother than traditional steel balls. The key advantage of ceramic bearings is their lower friction, which reduces heat buildup during high-speed operation, allowing for higher RPMs. This makes ceramic bearings ideal for spindles that need to maintain extremely tight tolerances at high speeds, such as those used for detailed aluminum or fine woodwork.
In addition to their frictional advantages, ceramic bearings also have superior heat resistance and longevity compared to their steel counterparts. This is particularly useful in applications where spindles are run continuously for extended periods. Additionally, their ability to handle both radial and axial loads with minimal wear makes them highly effective in high-stress environments.The downside to ceramic bearings, however, is their cost—they are significantly more expensive than both ball and tapered roller bearings. For hobbyists or light industrial applications, this investment may not be justifiable, but for operations that demand high precision and speed, ceramic bearings are an excellent choice.
The type of bearings you choose should align with the demands of your CNC machine’s workload. For high-speed, high-precision applications—especially those involving intricate work on harder materials like aluminum—ceramic bearings are a worthwhile investment due to their superior heat resistance, reduced friction, and durability. On the other hand, for general-purpose machining tasks involving softer materials like wood or plastics, ball bearings are typically sufficient, offering good speed capabilities and reliability without the higher cost. If your CNC machine will be handling heavy loads or more demanding cuts, such as large aluminum or steel projects, tapered roller bearings are ideal for their ability to withstand both radial and axial forces, providing the stability needed for heavier operations.
Cooling System: Air Cooled or Water Cooled?
Heat management is a critical factor in spindle performance, particularly during extended use or when cutting harder materials like aluminum or steel. Excessive heat not only shortens the lifespan of cutting tools but can also lead to spindle failure, which is why an efficient cooling system is essential. Cooling systems are an integral part of the spindle, and every CNC owner faces the decision of whether to opt for a traditional air-cooled spindle or a more advanced water-cooled option.
Air Cooled Spindles: A Simple Solution
Air-cooled spindles use built-in fans or heat-dissipating fins to manage the heat generated during operation. The fans circulate air around the spindle motor, helping to cool it and prevent overheating. A notable feature of air-cooled spindles is their rectangular shape, which accommodates the fans and airflow system. One of the key benefits of these spindles is their simplicity—they don’t require an external cooling setup, making installation and maintenance much easier. However, they tend to be noisier due to the constant fan operation, and they can struggle with heat management during extended or high-intensity machining tasks. While air-cooled spindles are well-suited for shorter tasks or lighter workloads, they may not be the best choice for heavy-duty or continuous operations where heat dissipation is critical.
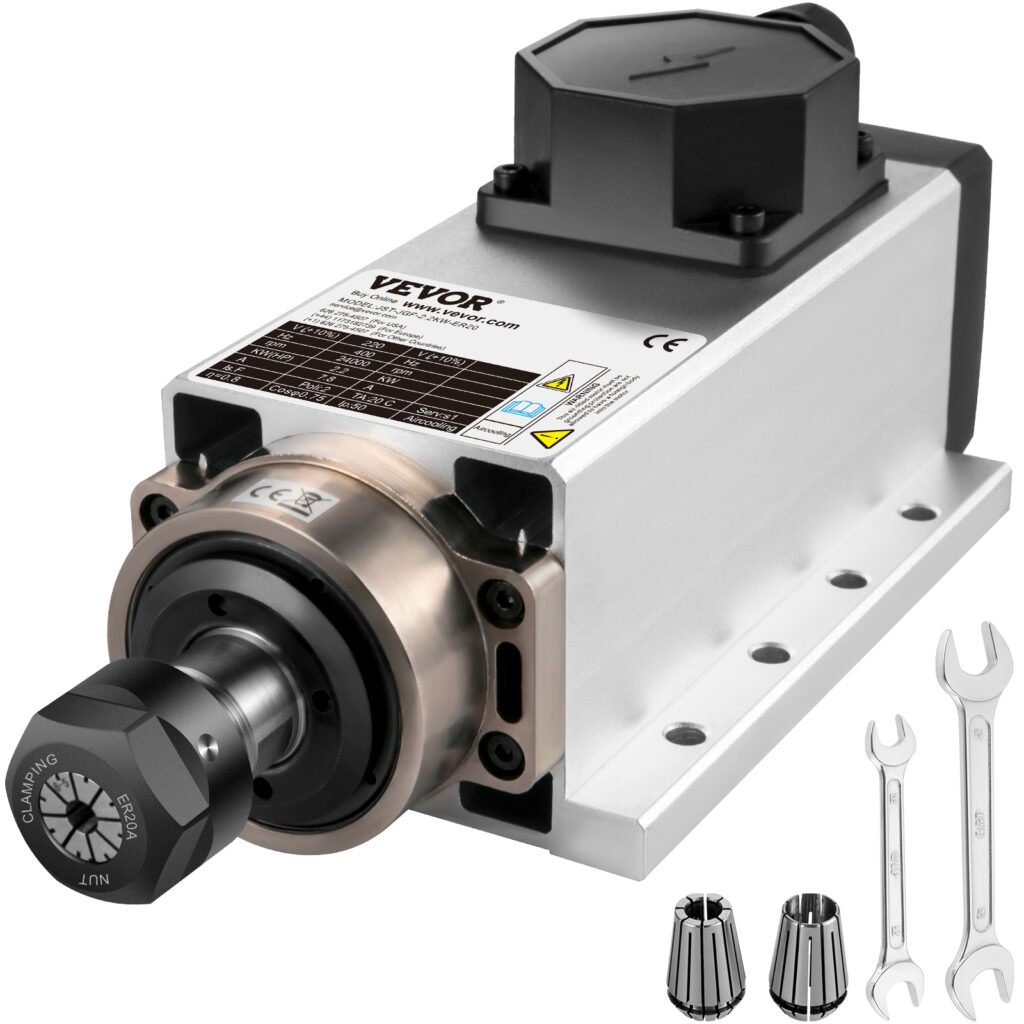
Water Cooled Spindles: A Complicated Superior Alternative
Water-cooled spindles utilize a closed-loop water system to regulate temperature, offering superior cooling compared to air-cooled alternatives. These spindles are typically circular in shape, which optimizes water circulation around the spindle housing. Water-cooled spindles are particularly effective for high-RPM operations or long-duration machining, where efficient heat management is essential. Additionally, they operate more quietly than air-cooled spindles since they lack fans. However, water-cooled systems require more complex setups, including a pump, reservoir, and tubing for water circulation. While these systems excel at maintaining cooler operating temperatures, they demand regular monitoring to prevent cooling failures, which can lead to rapid overheating. Despite the added complexity, water-cooled spindles are the preferred choice for demanding and long-running CNC tasks due to their enhanced cooling efficiency.
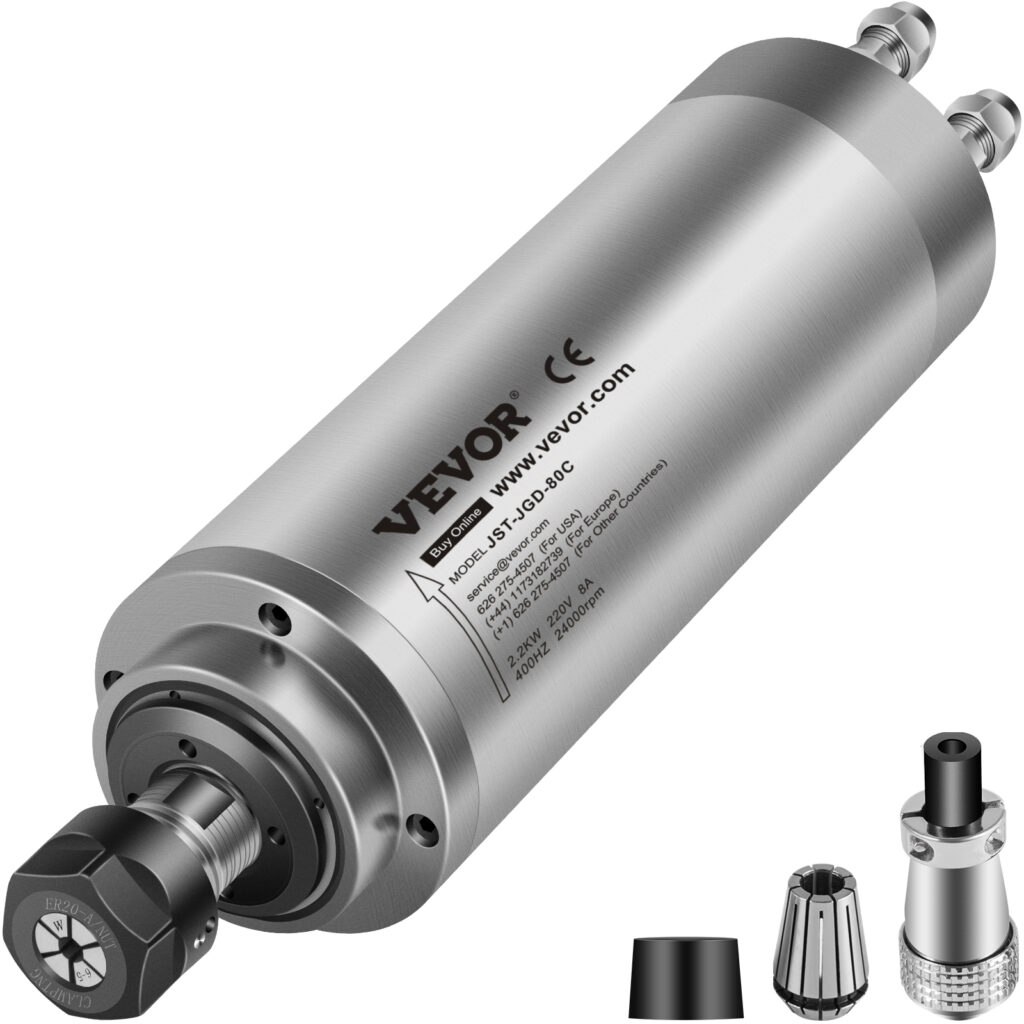
Key Takeaways
- Spindle Size Selection: Understand that spindle power should align with your project needs. Smaller spindles are suited for light materials, while mid-range spindles offer versatility for various materials, including aluminum. Always consider the material and task when choosing spindle power.
- Bearing Choice Drives Precision: The type of bearing directly affects spindle performance and longevity. Choose ball bearings for general use, but if you’re dealing with heavy-duty tasks or require high precision, tapered roller or ceramic bearings will provide the necessary stability and durability.
- Cooling is Critical for Spindle Longevity: Cooling systems play a major role in spindle efficiency. For long or demanding operations, water-cooled spindles provide better heat management. However, air-cooled spindles are simpler and may suffice for lighter tasks, depending on your operational needs.
Upcoming Articles Related To Spindles
In this article, we will dive deep into spindle collets and end mills, exploring how these two elements directly influence the precision and versatility of your CNC machine. Spindle collets are crucial for securely holding the tool in place, reducing tool runout, and ensuring cutting accuracy. End mills, on the other hand, determine the kind of cuts you can achieve, from roughing out large amounts of material to fine engraving work. Understanding the different collet sizes and end mill types will enable you to not only select an optimal spindle but also optimize your machine’s performance for the specific materials and designs you intend to work with.
This article will focus on the critical balance between spindle speed and feed rate, and how this directly affects the quality and efficiency of your CNC machining. Achieving the right combination is essential to prevent tool wear, burning, or poor surface finishes. We’ll break down the concepts behind cutting speed, spindle RPM, and feed rate, while providing guidelines to help you match these parameters to the material and tools you’re using. Proper understanding of these elements is key to maximizing your machine’s productivity while minimizing costly mistakes.
This article will focus on the relationship between material removal rate, power systems, and machining time, and how they impact the performance of your CNC machine. We’ll explore how different power systems can handle different spindle sizes and the diminishing returns of increasing power with respect to machining time. By examining these key factors, we’ll provide insights into balancing power, time, and material efficiency to optimize your CNC projects.
This article explores the relationship between spindle power and different milling operations, focusing on power-intensive tasks like slotting and plunging. We discuss key techniques such as ramp entry and chip evacuation to optimize performance, as well as the benefits of down milling and advanced toolpath strategies like trochoidal milling.
In these final articles, we will bring together all the key concepts from the previous discussions to create a comprehensive spindle selection guide. We’ll review the essential factors like spindle power, collet size, feed rates and material removal rates, ensuring that you can make an informed decision for your specific CNC setup. Additionally, we’ll dive into charts and performance data, analyzing different spindle options based on the criteria we’ve established throughout this series. These articles will serve as a step-by-step guide to finding the most optimal spindle for your machine, taking into account your material types, cutting requirements, and overall machine design.
In this article, we will explore the different methods of controlling spindle speed and power in CNC machines. Whether you’re using manual controls or integrating sophisticated variable frequency drives (VFDs), the way you manage your spindle’s operation can have a significant impact on both precision and efficiency. We’ll look at different control options, automation possibilities, and the pros and cons of each system, providing you with the knowledge to choose the right control system for your CNC build. Effective spindle control is critical for consistent performance, tool longevity, and achieving precise results in your machining tasks.