After examining the essential aspects of spindles—such as size, cooling, and bearings—it’s time to focus on one of the most critical components in the CNC machining process: the end mill. End mills are the cutting tools that directly shape your workpiece, and understanding their types, materials, and cutting strategies is key to achieving precision in your projects. In this article, we’ll delve into the various end mill types, flute configurations, and cutting techniques, all of which play a pivotal role in determining your CNC machine’s performance, efficiency, and final output quality.
End Mills: The Essential Cutting Tools
In CNC machining, end mills are the primary cutting tools that remove material from the workpiece to create the desired shape. The selection of correct end mill plays a critical role in determining the quality of the cuts, the types of materials you can machine, and the overall performance of the CNC system. Different end mills are designed for specific materials, cutting strategies, and project needs. As such, understanding the types of end mills, their geometry, and their interaction with the material is essential for optimizing your machine’s efficiency and output.
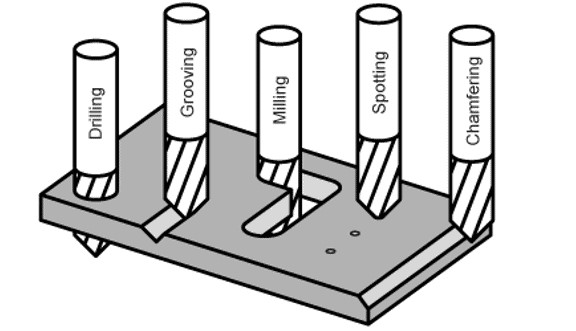
Difference Between Drill Bits and End Mills
One of the first distinctions to make when discussing CNC tooling is the difference between drill bits and end mills. While both are essential tools for material removal, they are designed for very different applications and have unique characteristics.
Drill Bits are specifically designed for drilling vertical holes into materials. They have a sharp point at the end to help them bite into the material and a helical flute to evacuate chips. Drill bits are only capable of cutting in the axial direction (up and down) and typically produce cylindrical holes. They’re not designed to cut horizontally, so their use is limited when it comes to side milling or surface profiling.
End Mills, on the other hand, are much more versatile. They are designed to cut not only axially like a drill bit but also laterally, allowing for complex machining tasks like profiling, slotting, facing, and contouring. End mills come in various shapes and sizes, each suited for different applications. Unlike drill bits, they do not have a sharp point at the end, allowing them to mill surfaces flat or along contours.
The versatility of end mills makes them a preferred tool for CNC milling applications. While drill bits may be occasionally used in CNC operations for creating vertical holes, end mills are the primary tool used for machining various features, offering greater flexibility in the types of cuts and shapes they can produce.
Anatomy of an End Mill
Understanding the various parts of an end mill is crucial for selecting the right tool for your CNC operations. As shown in the diagram, an end mill is composed of several key components that each play a role in the tool’s performance. The cutting diameter (D) is the first aspect to consider, as it determines how much material will be removed in a single pass. A larger diameter allows for higher material removal rates (MRR) and increased cutting efficiency but also requires a more powerful spindle to handle the greater cutting forces generated. The cutting edge is the active part of the tool that engages with the material to perform the cutting action. Its shape—whether straight, curved, or angled—affects the manner in which the material is cut and the surface finish quality.
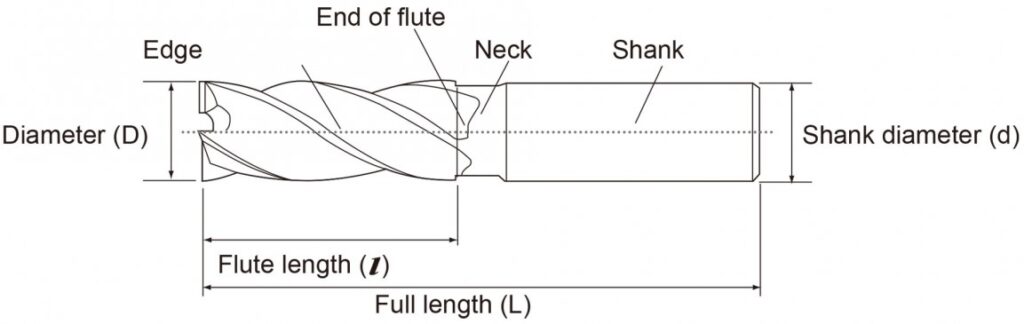
The flute length (l) is the section of the end mill that contains the cutting edges and dictates the maximum depth of the cut. While longer flute lengths enable deeper cuts, they can also reduce the tool’s rigidity, potentially leading to increased vibration and deflection. The end of the flute marks the maximum effective cutting depth. If this limit is exceeded, the tool could suffer damage, and the resulting surface finish may be compromised. Directly adjacent is the neck, which is typically thinner than the shank and provides clearance for deep cuts. While the neck does not engage in cutting, it prevents interference with the workpiece or fixture during operation.
The shank is the part of the end mill that is clamped into the spindle’s collet, ensuring a firm grip for precision and stability during cutting. I will be dedicating an entire article on collets, stay in tune! The shank diameter (d) must match the collet size to ensure a secure fit, and larger shank diameters offer more rigidity and reduced deflection, which is crucial for heavy-duty operations. Lastly, the full length (L) of the end mill, from the cutting edge to the back of the shank, determines how deep the tool can penetrate into the material. However, longer tools increase the risk of deflection, especially if the flute length is too long in relation to the shank diameter. By understanding these components, machinists can select end mills that suit their specific tasks, optimizing both performance and tool longevity. In the following section, we’ll explore the different types of end mills and how they fit into various machining tasks.
Common End Mills & Purpose
Square End Mill (Straight Edges)
Incredibly versatile and one of the most common types used in CNC machining. They are particularly useful for making flat cuts and machining straight edges, as well as for operations like slotting and profiling. The sharp, square corners allow for precise 90-degree cuts, which is crucial when creating detailed parts with clean edges, especially in both wood and aluminum. Their ability to plunge straight into the material makes them essential for tasks that require precise depth control, making them a staple for almost any CNC project.

Ball Nose Mill (Rounded Surfaces)
Designed for more intricate 3D contouring work, including engraving. The rounded tip allows for smooth, curved finishes, which is ideal for complex surface geometries, like molds, models, or decorative projects. These end mills are also great for minimizing tool marks because they produce smoother transitions between cuts. While square end mills are perfect for sharp edges, ball nose mills are critical for finishing rounded surfaces and sculpting detailed parts in both wood and soft metals, making them valuable when precision is needed over varying depths and curves.
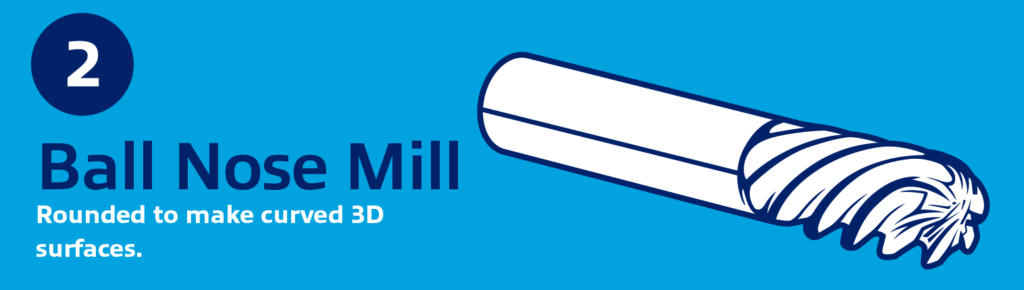
Roughing End Mill (Irrelevant For Hobbyist CNCs)
While excellent for fast material removal in industrial settings, may not be suitable for my intended CNC build. These tools require significant spindle power and a highly rigid machine structure to operate effectively, as they place considerable stress on the machine due to their aggressive cutting action. Given that my CNC machine is designed for a range of materials like wood and aluminum, but with a focus on precision and versatility rather than brute force material removal, roughing mills are not the best fit.
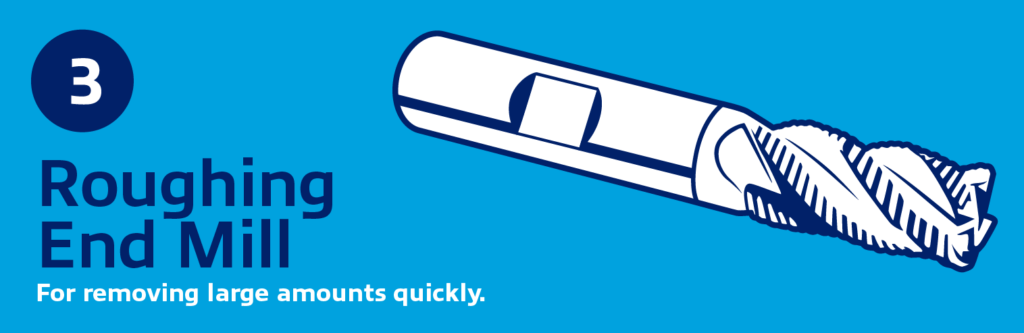
Diamond Router (Irrelevant For My Use)
Diamond router end mills are primarily used in industrial applications for cutting composite materials like carbon fiber or reinforced plastics, offering long tool life and efficiency for abrasive materials. However, these end mills are not necessary for my CNC machine due to their high cost and my lack of need for composite cutting projects. Given that my machine is designed for working with materials like wood and aluminum, investing in such specialized and expensive tools would be unnecessary and impractical for my intended applications.
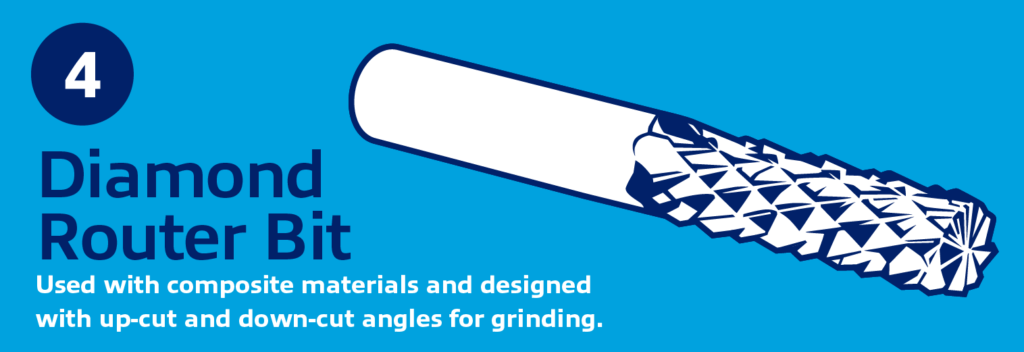
Indexable Face Mill (Irrelevant For Hobbyist CNCs)
Indexable face mills are commonly used in industrial settings for large-scale material removal and surface flattening, thanks to their efficiency and cost-effectiveness with replaceable inserts. However, they are both expensive and beyond the needs of my CNC machine. Since I don’t plan on tackling projects that require this level of power, and my machine lacks the spindle power and rigidity to handle such demanding tasks, the high cost of these tools makes them an impractical choice for my build.
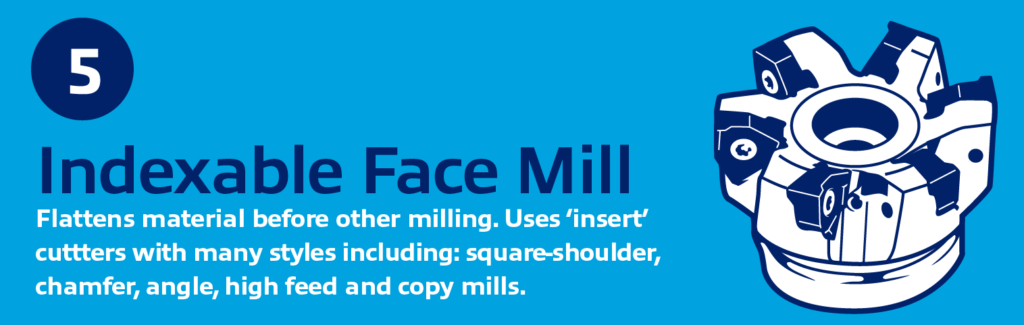
Chamfer Mill (Beveled Edges)
Primarily used to create beveled edges or remove sharp corners from a workpiece. These mills are designed to cut at angles, typically 45 degrees, and are essential for tasks that require smooth transitions between surfaces. Chamfering is often done for aesthetic purposes or to prep a part for assembly. Given that chamfer mills require less cutting force compared to roughing mills, they are well-suited for my CNC machine’s intended use. Since I plan to work with wood and aluminum, chamfer mills will allow me to add finishing touches without overstressing the spindle or frame.
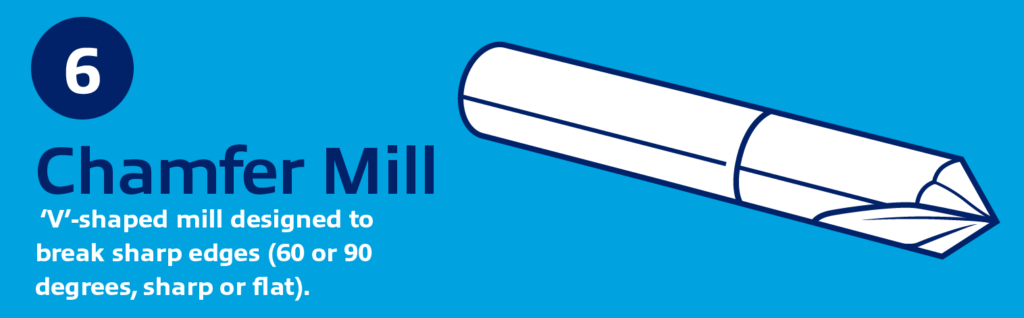
Indexable Face Mill (Irrelevant For My Use)
Used to create internal or external threads in a workpiece. Unlike taps, which are limited to one specific size, thread mills offer the flexibility to cut various thread sizes with the same tool, depending on the machine’s programming. This flexibility makes them an excellent option for CNC machines capable of detailed, precision work. However, thread milling can be demanding on the spindle and machine rigidity, especially when working with harder materials. While my machine may handle aluminum and wood well, the precision required for threading metals, especially at finer pitches, could pose a challenge if the machine’s rigidity is not up to par. For now, thread mills are not a tool I expect to use often with my machine.
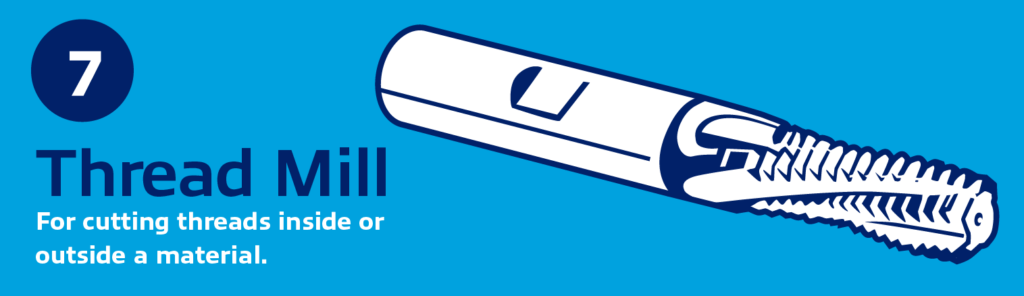
Drill Mill (Drilling & Light Milling)
Drill Mills combine the functionality of both a drill and a mill. These tools are particularly useful when you need to drill holes and then immediately mill without changing tools, saving time in a production run. Drill mills feature a pointed tip, allowing them to start holes, and they can also perform light milling operations. However, they are not designed for heavy-duty milling tasks, so their cutting forces are moderate. For my CNC build, drill mills could be a versatile addition, particularly for small projects or lighter milling tasks in aluminum or wood.
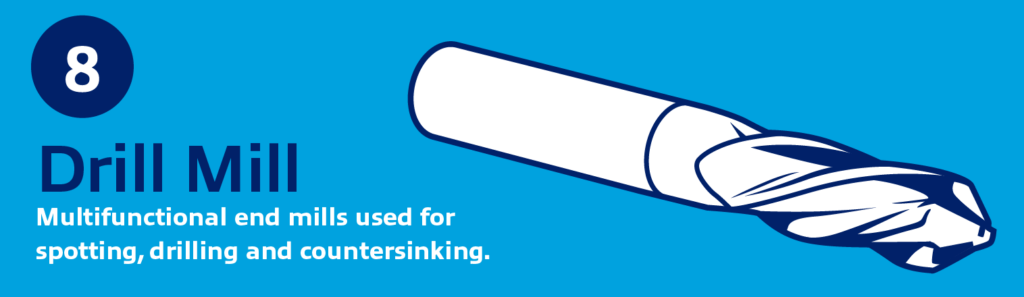
What's Flute in Mills?
Flutes are the grooves or channels along the cutting edge of a end mill that allows for material removal and chip evacuation during cutting. The number of flutes on a end mill significantly affects its cutting performance, surface finish, and chip evacuation, making it an important factor in end mill selection. Summarizing the sections below, the general rule is: Harder materials require more flutes for smoother cutting, while fewer flutes provide more space for chip evacuation, making them ideal for softer materials. Let’s discuss this in a greater depth.
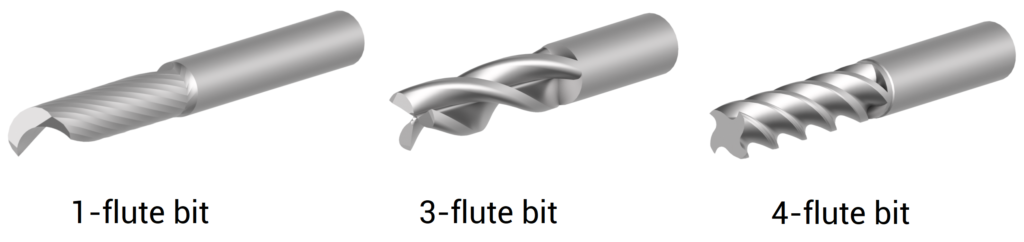
Why Flute Matters
The number of flutes on a end mill plays a crucial role in chip evacuation, which is especially important when working with softer materials. In materials like wood, plastic, or aluminum, where larger volumes of chips are produced, end mills with fewer flutes—such as 1-flute or 2-flute end mills—allow more space for the chips to escape. This prevents clogging and overheating, which can damage both the tool and the workpiece. In contrast, end mills with more flutes, such as 4-flute or higher, have less space for chip removal, making them more suitable for materials that produce fewer chips, like steel or titanium.
Cutting speed is another factor that is influenced by the number of flutes. End mills with fewer flutes can remove material faster because they allow for a higher chip load per flute, meaning more material is removed with each pass. This makes 1-flute and 2-flute end mills ideal for rapid material removal in applications like roughing or when working with soft materials. However, more flutes generally lead to a smoother surface finish, as the cutting forces are spread out across more edges. For operations requiring fine detail or a smooth finish, such as finishing passes on harder materials, end mills with more flutes—3-flute or 4-flute—are preferable, even though they may cut more slowly.
Material hardness also dictates the number of flutes required. Harder materials, such as steel or hardwood, benefit from end mills with more flutes. The additional cutting edges distribute the forces more evenly, reducing wear and tear on the tool and providing a cleaner cut. Softer materials, on the other hand, typically perform better with fewer flutes, as the larger chip clearance prevents clogging and allows for efficient cutting.
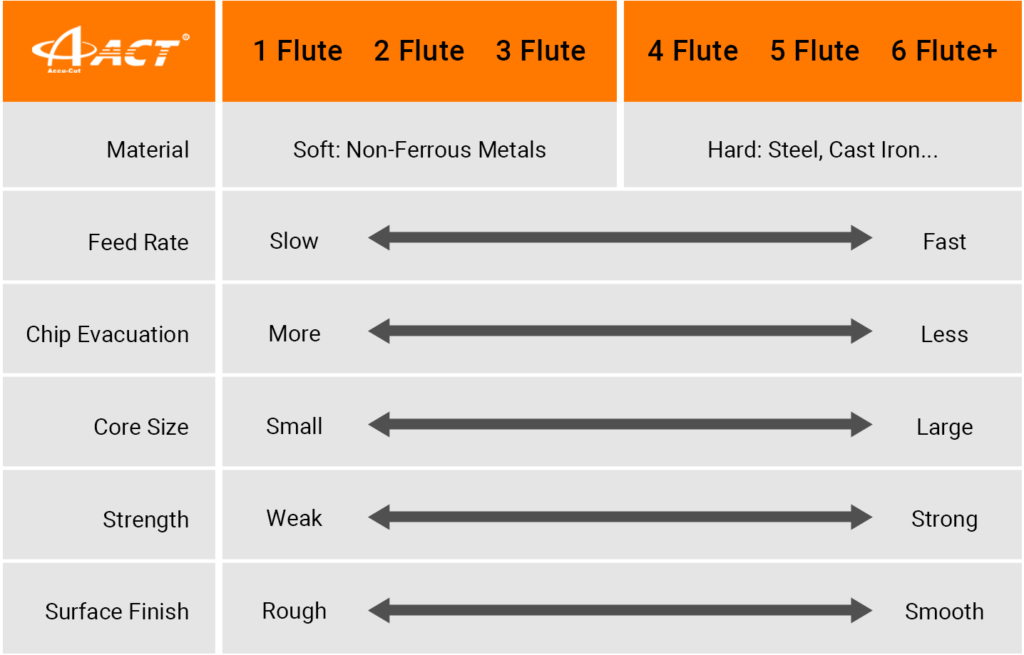
Below, I’ve provided a summary of the flute count based on my understanding of different materials, operations, and their specific requirements. This breakdown will hopefully help you guide the selection of the proper end mill for each job.
General Materials
Soft Wood: 1 Flute
Plastic: 1 Flute
Foam: 1 Flute
Hardwood: 1-2 Flutes
Metals
Aluminum: 1-2 Flutes
Brass: 2-3 Flutes
Copper: 2-3 Flutes
Steel: 4+ Flutes
Titanium: 4+ Flutes
Milling Processes
Roughing: 1 Flute
Engraving: 2 Flutes
Finishing Operations: 3-4 Flutes
Difference Between Upcut & Downcut End Mills
Upcut and downcut end mills refer to the direction in which the flutes of the cutting tool move the material during cutting. These terms are essential in understanding how to achieve optimal surface finishes and material ejection, especially in woodworking and plastics.
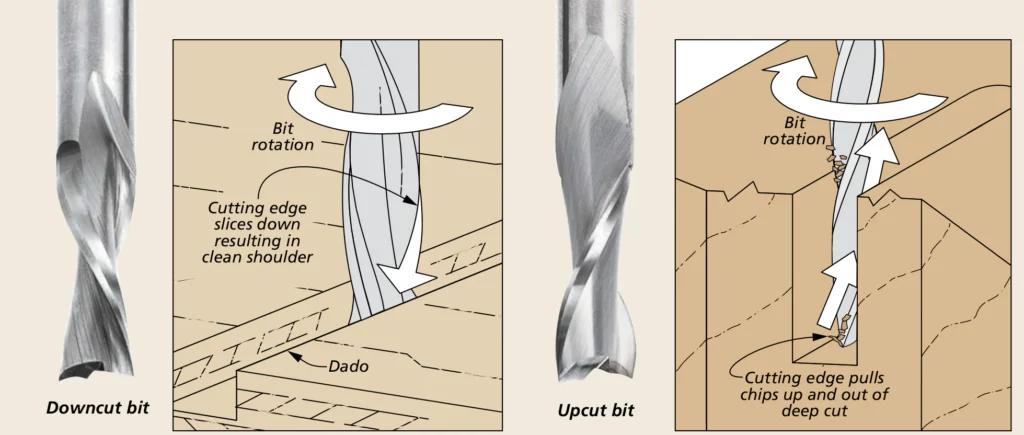
Upcut End Mills
Upcut end mills work by removing material in an upward direction, pulling the chips away from the cutting surface. This ensures excellent chip evacuation, which prevents clogging and helps maintain a cooler cutting environment. The efficiency of chip removal makes upcut end mills ideal for deep cuts, such as pocketing or slotting operations, and for hard materials like aluminum where heat management is critical. However, the upward motion of these end mills can result in splintering or tear-out on the top surface of the material, particularly when working with softer woods or laminated materials. Common types of upcut end mills include flat end mills, ball nose end mills, and spiral router end mills.
Downcut End Mills
In contrast, downcut end mills push the chips downward, pressing them back into the material. This results in a clean top surface with minimal tear-out, making downcut end mills particularly useful for working with plywood, MDF, and laminate materials. However, because the chips are pressed downward, they can accumulate in deeper cuts, leading to potential overheating or burning. As a result, downcut end mills are best suited for shallow cuts where surface finish is important, such as engraving, shallow pocketing, and edge trimming. They are commonly used in V-end mills for engraving, chamfer end mills, and straight router end mills.
Choosing the Right End Mill Material
High Speed Steel (HSS)
CNC end mills are typically made from a few key materials, each with unique properties suited to specific tasks. High-Speed Steel (HSS) end mills are the most affordable option and are commonly used for softer materials such as wood, plastics, and some metals. While HSS end mills offer a cost-effective solution, they tend to wear out faster, especially when used on harder materials, which makes them less durable than other options.
Carbide
Carbide end mills, on the other hand, are more expensive but offer significantly greater durability and wear resistance. These end mills can handle higher cutting speeds and are ideal for machining metals like aluminum and other harder materials. Their ability to maintain sharpness over extended periods allows for more precise cuts, making them a preferred choice for more demanding projects.
Titanium Nitride Coated (Irrelevant For My Use)
Coated end mills, which have a protective layer such as titanium nitride (TiN) or diamond-like carbon (DLC), further enhance durability by reducing heat buildup during cutting. These coatings make end mills especially useful when working with tough materials like steel or high-temperature alloys, extending the tool’s lifespan and improving performance under challenging conditions. These end mills are irrelevant in our use case as we do not plan on milling any hard metal where we would need a heat specific coated end mill.
Choosing an End Mill Based on Cutting Diameter
When choosing an end mill, the cutting diameter is a critical factor that impacts material removal, surface finish, and cutting forces. However, this selection is not solely about the diameter itself; it must be matched with the shank size to ensure compatibility with the spindle’s collet. For example, let’s consider two end mills with the same shank size of 1/2″, but different cutting diameters—1/4″ and 3/8″. The decision between these two depends on the requirements of the specific milling operation.
A 3/8″ diameter end mill is capable of removing more material in a single pass, thus increasing the material removal rate (MRR). This is particularly advantageous for roughing operations, where faster cutting and higher productivity are desired. Additionally, the increased diameter offers greater rigidity, which reduces the likelihood of tool deflection, especially when machining harder materials. This results in a smoother surface finish and improved dimensional accuracy. The larger cutting diameter also generally allows for more robust cutting forces, making it ideal for more aggressive milling tasks.


Conversely, a 1/4″ diameter end mill is more suitable for operations requiring detailed work, intricate features, or small pockets. Although it engages less material during each cut and generates lower cutting forces, it provides better control for precision operations. This can be beneficial when working on projects that demand fine detail or when using a CNC machine with a lower spindle power. However, the smaller diameter is more prone to deflection during heavy cuts, which can impact accuracy and surface finish.
In general, the best practice is to use a larger diameter end mill if the goal is to maximize efficiency and remove large amounts of material quickly. However, for precision work and small-scale features, a smaller diameter is preferable. Ultimately, the selection depends on the specific machining task, the material being worked on, and the capabilities of the CNC machine. Choosing the right diameter, in conjunction with a matching shank size, ensures stability, efficiency, and high-quality results in CNC milling operations.
Key Takeaways
- End Mill Variety: The type of end mill you choose has a direct impact on the quality of your cuts. Square end mills are ideal for basic slotting and cutting, while ball nose mills excel in detailed 3D work. Specialized end mills, like chamfer, cater to specific applications like beveling edges.
- Flutes and Their Function: The number of flutes on an end mill affects chip evacuation, cutting speed, and surface finish. For soft materials like wood or aluminum, fewer flutes (1-2) are preferred, whereas harder materials like steel require more flutes for efficient cutting.
- Upcut vs. Downcut: Upcut mills offer better chip evacuation but can cause splintering, making them ideal for deeper cuts and hard materials like aluminum. Downcut mills provide a cleaner finish on the top surface, especially useful for soft materials, laminates, or shallow cuts.
- End Mill Material: High-Speed Steel (HSS) is cost-effective and works well for soft materials, but carbide end mills provide greater durability and precision, especially when machining metals or harder materials.
- Diameter Selection Matters – Larger diameters offer rigidity, while smaller ones provide precision. Choose based on your machining needs.